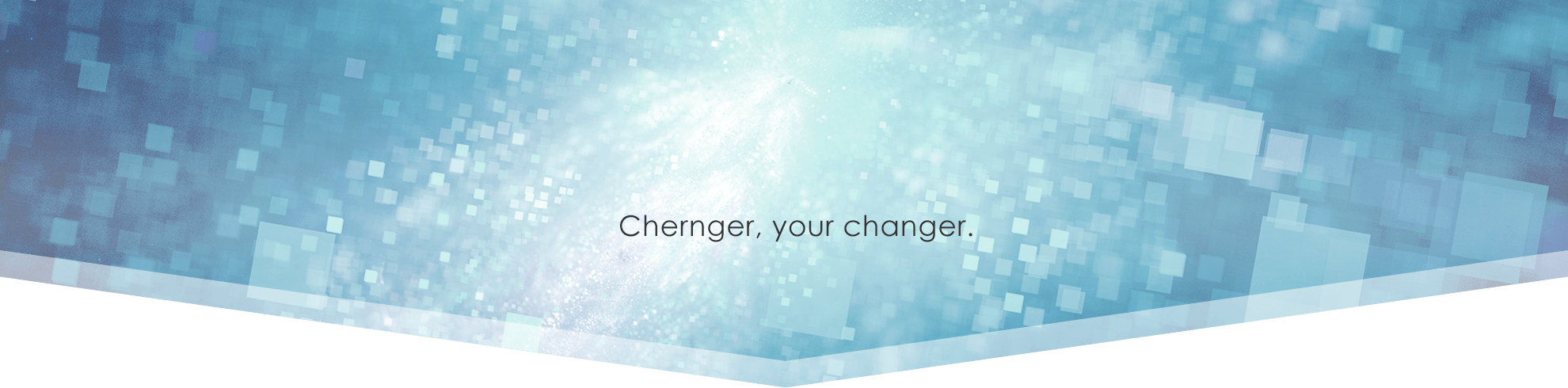
Evaluation of AOI Inspection Systems
Evaluation of AOI Inspection Systems
Usually a detection system has several key elements
Speed
Refers to how many samples are tested per minute. For example: 120 pieces/minute, 15 pieces/second or 4 meters/minute, etc.
Accuracy
The minimum defect or unit size that needs to be detected; for example, 0.05mm or 0.5um, etc. The usual detection accuracy is 0.05mm. The resolution of the camera only needs to be increased by at least 3 times to 10 times, which is 0.0166mm or 0.005mm. Because the camera pixels cannot be so sharp that the edge can be seen clearly with just one pixel, more than 3 pixels can have a correct judgment rate of more than 98%, and 10 pixels can have a stability of more than 99.7%. But the cost will increase several times, so the industry usually makes a trade-off of 3-5 times. If the detection accuracy is the same as the camera resolution, the measurement stability or accuracy can only reach 50%. This is a risk that people with no experience or limited funds may make.
False rate and overkill rate
Generally, for objects that can be detected by the naked eye, the error rate of human detection is about 1%, and the error rate of double human detection will be reduced to 2-3 parts per 10,000. Setting the allowable error rate of AOI detection at 1% is based on the concept of human substitution. The industry standard is between 1% and 0.3%, and the detection rate is 99% and 99.7%. This is a tall order. There is another concept to achieve this goal. Because the standard SOP is set by people. Some objects are easy to identify and others are difficult. The identification levels can be divided into three levels. Those that can be seen by anyone are Level C, those that require professional guidance to see defects are Level B, and those that only professionals can see are Level A. Generally, the detection rate of A-level AOI should be above 99.7%, that of B-level is 95%~90%, and that of C-level is 90%~85%. Such a definition can effectively resolve disputes over the expected value of AOI machine testing.
Field of view (FOV)
The detection object is 100%, and the camera’s FOV must be at least 110%-120%. It depends on the accuracy of the mechanism. The higher the accuracy of the mechanism and control, the closer it can be to 100%. For example, to detect an object of 20mm On the contrary, if the tolerance FOV is greater than 1mm, it is more appropriate to use 24mmX24mm. Some special detection technologies require FOV to be converted into a high depth of field in order to meet detection requirements. This technology was very valuable in the early days. With the development of lens technology, lenses with high depth of field can be obtained for a price. The FOV of a line scan camera can be viewed as line scan width x length (width length).
AOI system architecture and stability
The AOI system has five parts: A (camera + lens) B (light source) C computer D control system E mechanism. Among these five parts, the cable connecting the camera and the computer is also very important. It will have several interfaces: BNC (analog low speed) USB2.0 (low speed) GigE (medium speed) USB3.0 (high speed) USB3.1 (high speed) CAMERA LINK (high speed). Usually, the problem that is more likely to occur on high-speed systems during detection is the problem of missing frames, that is, more than 10 frames need to be calculated per second. However, because the calculation amount of each frame is different, it will cause the frame to be dropped and missed during detection when the speed is reduced. Usually, the system stress test needs to be done first. For example, if the computing power can reach 20 frames per second, the light source, mechanism and control system will be very stable when adjusted to 15 frames per second. High-speed, high-pixel cameras are usually equipped with high-speed interfaces, and the relative allocation of computing power is also very important. If you choose a package system such as (Omron, Keynes, Cones, etc.), you will be limited by the computing power of their models.
Generally, those who use self-developed OpenCV (Open Source Computer Vision Library) visual source code calculation library and developer’s tool library can choose to use CPU computing or MCU computing (acceleration card). to accelerate computing power. A good solution can increase the system’s processing of 2M photos from 10 photos/second to 100 photos/second. This depends on the experience and ability of the engineer.
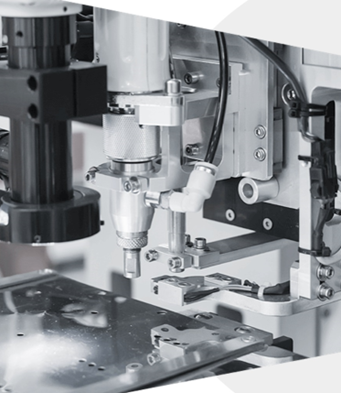
相關文章
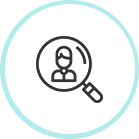
AOI 機台評估入門
通常有經驗的廠商在機台簽約開發時就會有一份標準格式的驗收報告。以確定交機驗收時不會有爭議,有個標準訂在那邊共同遵守。難免評估者在評估中產品生產初期沒有出現的瑕疵,或是客戶端臨時要求檢測的項目。有驗收標準就不會產生爭議。
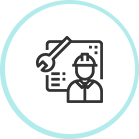
AOI檢測的光源技術
好的光源系統 通常需要一個很穩定的電源電壓調節器,可以容許電源有10%-20%的變動,但是輸出的交流AC 60HZ,其變動率要小於0.1% 。這樣的環境就可以確保量測的品質。
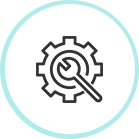
AOI檢測的光源技術-2(進階篇)
光源幾乎是能否檢測的關鍵門檻,有些物件像圓弧或半圓類的金屬件,檢測本身就是一個超高難度,通常要先有好的合適的光場之後,才有機會進到程式去編寫。
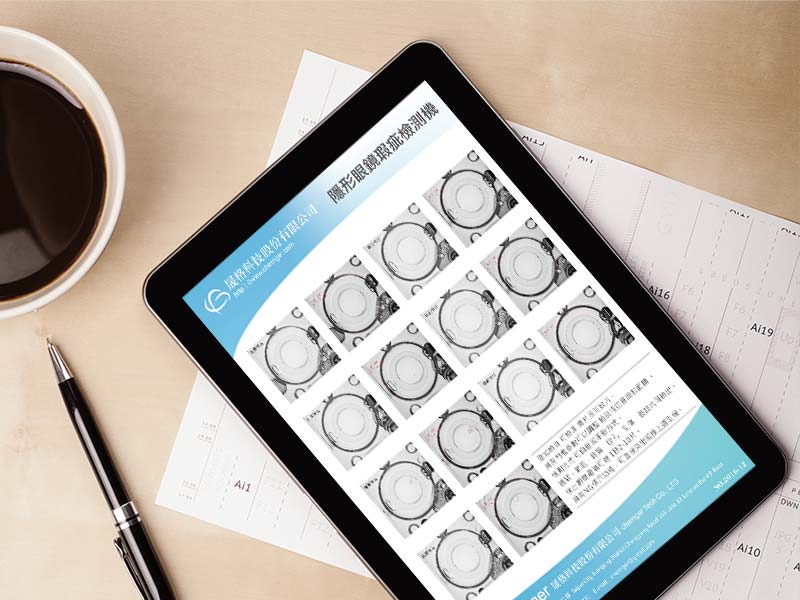